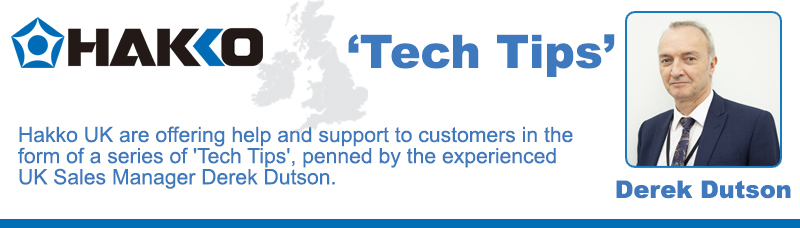
Top Tips To Optimise Your Soldering Process
To fully optimise peak performance of your soldering equipment, there are few guidelines that can easily be factored into your routine. For instance, to keep solder tips in tip top condition and reduce oxidation, we advise keeping the pre-set temperature of the soldering iron as low as possible to enable sufficient melting of the solder alloy and the production of a satisfactory soldered joint. We cannot stress enough the importance of keeping soldering tips clean for consistently good soldering results. In this issue of Hakko Tech Tips, we will look at some of the most frequently asked questions fielded regularly by our technical support team to help alleviate any of your questions. So, let’s take a closer look in our 5 tip format below:
1) Is it possible to solder without flux and what are the consequences of doing so?
It is theoretically possible in an inert atmosphere with absolutely no oxidation present but, in practice, highly unlikely. Flux is required to clean oxidation from the surfaces to be joined, reduces the surface tension of solder and forms a protective layer to prevent any further oxidation occurring. In most cases, if attempted, the solder will not wet the component lead and PCB, leaving a very poor electrical connection with little or no mechanical strength. So, we don’t advise attempting to solder without flux.
2) How can I judge how much heat to use? Is this just down to experience or are there some hard and fast rules?
Ultimately, this is down to experience and/or training. The minimum amount of heat should be used to produce a good soldered joint. A good starting point would be to set the solder station temperature to anywhere between 340 °C and 380 °C. Small solder joints with little thermal demand will require a low heat setting, whereas larger components, especially when connected to heavy ground planes, will require more. Selection of the correct solder tip will also aid thermal conductivity. The optimum sized tip should be used to replicate the size of component lead and PCB pad whilst the largest thermal mass will help maintain tip temperature and, potentially, use of a lower tip temperature.
3) Why do solder joints fail?
Solder joints tend to fail for two reasons; poor quality and external forces. If poor quality components, PCBs or materials are used, it will always be difficult to achieve and maintain satisfactory results. Qualified Operators recognise how long is required to produce a good solder joint. The time taken (just a few seconds) will allow for pre-heating, flux activation, cleaning of the surfaces, melting/flow of the solder alloy and formation of the correct width intermetallic layers. If these intermetallic layers are too thin then this will produce a weak joint, conversely being too thick will produce a brittle joint. Production of any of the aforementioned joints may be fit for purpose during manufacture. However, most electronic assemblies are then subject to external forces in the field. These could be extreme temperature cycling, shock, vibration, corrosive atmospheres, or any combination of each. This is usually when solder joints will fail mechanically and/or electrically.
4) Do smaller tips naturally transfer less heat?
Typically, smaller tips transfer less heat even though the solder station is set at the same temperature. Tip selection is a critical consideration during any soldering application. The physical size should be as close as possible to the PCB and components to be soldered. A closely matched contact area will be much more efficient in transferring heat to the workpiece. At the same time use of a closely matched tip with the highest thermal mass will ensure better thermal stability and may allow a lower set point to be used.
5) How many different types of solder are there?
There are many different solders wires available, probably hundreds. Each can be classified by types of alloy, flux, physical diameter and flux content. Common alloys utilised are Tin/Lead, Tin/Silver, Tin/Silver/Copper and Tin/Copper. Each manufacturer is likely to have their own flux recipes. Physical sizes are usually (0.3, 0.6, 0.8, 1.0, 1.2, 1.6mm) in diameter, although these may vary slightly by manufacturer. Flux contents tend to be between 2% and 3%.
Hakko’s soldering products are globally recognized for their proven solutions that really do exceed expectation. Dedicated to meeting the ever-increasing demands for maximum soldering performance and improving work-in-progress for customers across the world, Hakko welcomes feedback from our customers and potential new customers, so please do talk to one of our team if you have any questions. Look out for next month’s Hakko Tech Tips where we will be bringing you more top tips on maximising your soldering process.